Boiler Repair Technicians: Who Fixes Your Heating System and Why It Matters
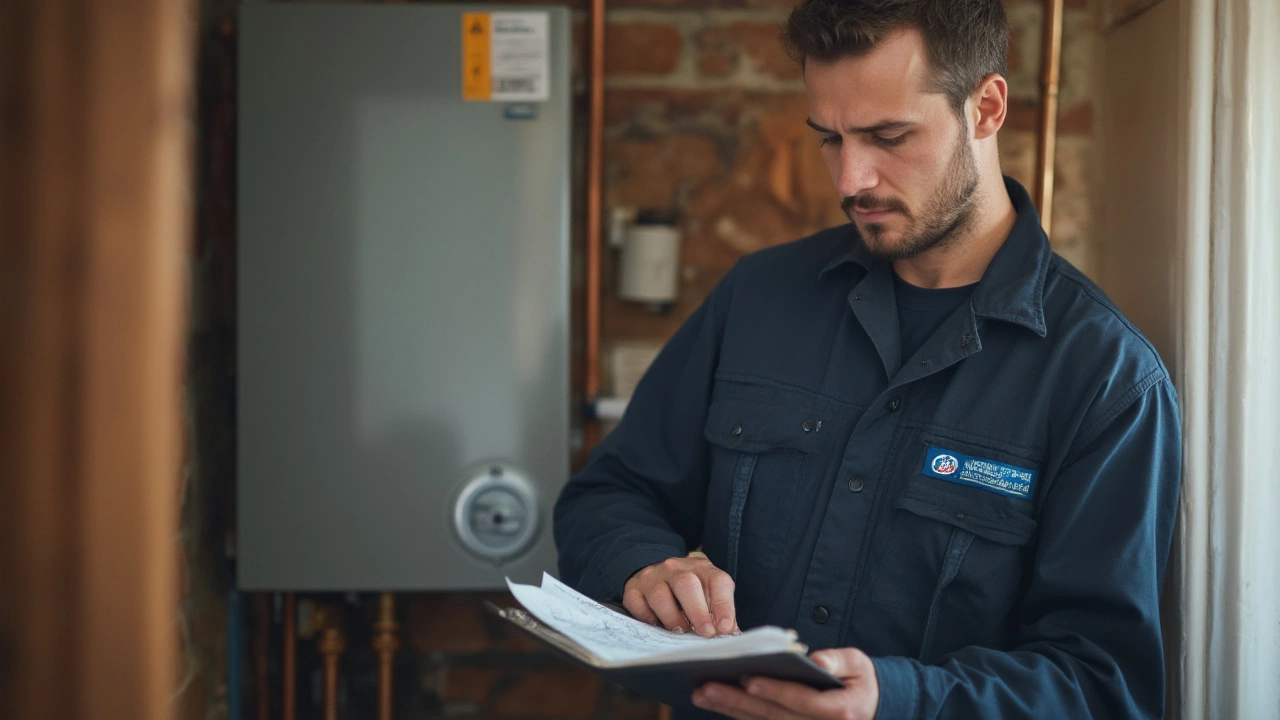
Holiday season chills and the relentless hum of a cold snap have a funny way of exposing a household's weakest point fast—the boiler. But who's the hero that shows up to work magic on your heating system when the house turns ice-cold overnight? Spoiler: it's never the 'handy guy from down the street' if you're wise. The real fixers are a highly specific breed: the boiler repair technicians, also known officially as certified gas engineers or heating engineers, and sometimes, old-school plumbers who've specialized. Their world is a mix of grit, grit, and more grit, spinning wrenches in cramped basements, piecing together lost heat, spotting hidden leaks that would make most people panic. Ever see a person walk into a freezing utility room grinning? That’s your boiler tech—just another day at the office.
The People Who Fix Boilers: Old School Versus New School
If you ask any seasoned landlord or homeowner with gray in his beard, the 'boiler man' stereotype hasn’t changed for decades—a burly, no-nonsense problem solver. But that’s only half the story now. Modern boiler technicians can look like anyone: young, female, tattooed, or suit-wearing. It comes down to intense training and killer instincts for danger. Let’s get this straight: in the UK, for example, anyone touching a gas boiler legally must be Gas Safe Registered. In the States, it's all about HVAC certifications from agencies like NATE or local unions. Not just a slip of paper—getting certified means months or years of classroom learning, real-world troubleshooting, and serious safety drills. Boiler repair isn’t for the faint-hearted. You’re dealing with pressurized systems, sometimes burning fossil fuels, which, if handled wrong, turn basements into news headlines.
Most of today's boiler techs cut their teeth on basic plumbing or general heating gigs before specializing. It’s not unusual for the best in the business to have ten or twenty years under their belts, but you’ll see younger faces too, thanks to the rise in eco-heating systems and the winding down of old trades. Women are pushing into the scene with top marks—one UK trade college reported a 25% rise in women getting heating certifications since 2021. So while the image of the 'man with the monkey wrench' sticks around, the field is way broader. There’s a universal requirement, though: guts under pressure (literally), and nerves to troubleshoot in the dark, damp, or biting cold with time ticking.
Training for boiler repair is relentless. Apprentices typically shadow veterans for one to three years, sweating through cramped spaces and learning real-world lessons very fast. Trade colleges load them with electrical know-how (wiring for sensors and thermostats), chemistry basics (water pH affects boiler scaling), and even people skills, since half the job is talking homeowners off the ledge. It’s boot camp for the mechanically gifted but socially savvy.
Don’t forget, experience brings muscle memory—the kind that quickly spots a burnt-out solenoid just by the smell, or catches the early gurgle of air in a system. Seasoned techs are obsessed with their toolkits: pressure testers, leak detectors, thermal cameras, and smartphone apps logging boiler codes. Most carry spares for common faults, like air valves and flame sensors, all tucked into vans that double as mobile workshops. But behind every tool is a sharp mind—boiler breakdowns rarely hand over obvious clues. The art is in teasing out what’s wrong with limited info, tricky homeowners, and equipment built to hide its disappointments.
What Skills and Qualities Set a Boiler Technician Apart?
Everyday life for a boiler tech reads like a highlight reel of Murphy’s Law. Something will go wrong—it’s just a matter of when. So, what makes a truly great boiler repair technician? First, unshakeable attention to safety. The consequences of sloppiness aren’t small—they’re catastrophic. In the UK alone, improper boiler repairs cause hundreds of carbon monoxide incidents every year. One mistakenly missed seal can lead to invisible, deadly gas seeping into homes.
Second: technical smarts that go way beyond just 'fixing stuff.' These pros understand not just how a boiler ticks, but why. They know the science of water chemistry, how oxygen causes corrosion, and how mineral buildup silently chokes efficiency. As heating systems get smarter, techs keep up with diagnostic software, Bluetooth tools, and apps that let them crack complex code errors—one misplaced sensor can take down an entire system. They’re part detective, part engineer, part therapist when homeowners spiral into panic.
Communication skills? Non-negotiable. Boiler problems make people anxious—the showers go cold, radiators clank, and bank accounts tremble at the thought of a full replacement. The best repair techs calm the room, walking customers through options, explaining why some fixes are urgent and others can wait, and showing that the right repair now stops an expensive disaster later.
Physical toughness is a must. Watch a seasoned technician wedge himself into a crawlspace filled with cobwebs, wrestling ancient pipework, headlamp flickering as he checks for rust. They need real stamina—hauling heavy flue pipes, crawling up ladders, braving chilly attics or waterlogged basements at midnight just to keep a family warm.
Here’s a table from the Heating and Hotwater Industry Council (HHIC) summarizing top skills and how often homeowners say they matter when picking a technician:
Skill/Quality | Percents Homeowners Consider 'Essential' |
---|---|
Gas Safety Registration | 95% |
Experience (5+ Years) | 82% |
Clear Communication | 77% |
Technical Knowledge | 83% |
Punctuality | 64% |
Physical Endurance | 59% |
From those numbers, you can see it's not just about who knows how to turn a wrench—it's the full package. The best boiler techs build their reputation one reliable call-out at a time, earning trust in emergencies by showing up, fixing it right, and making sense of complicated systems without scaring people silly.
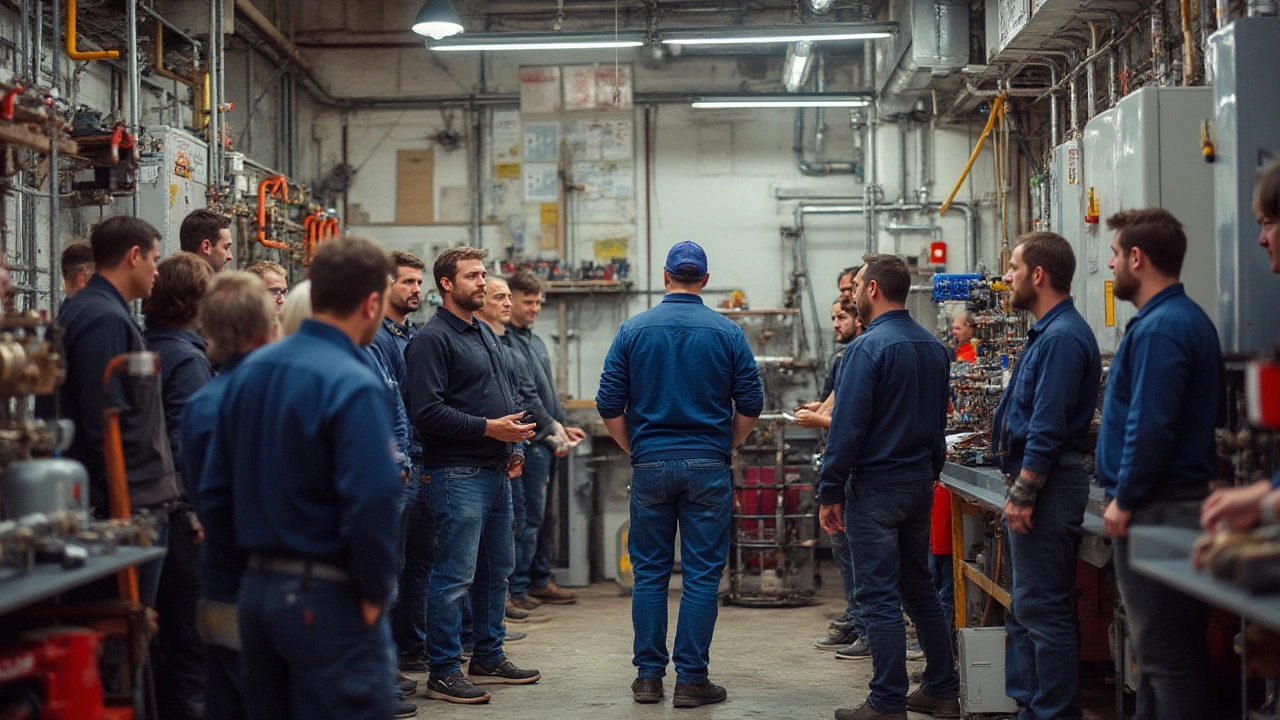
What Does a Day Look Like for a Boiler Repair Technician?
If you’ve ever wondered what a day in the life of a boiler expert looks like, think less 'office cubicle' and more 'adrenaline with a side of grit.' Picture a winter morning—the phone starts ringing before daylight. Scheduling is a Tetris game: one emergency in a row of three annual services, plus a surprise boiler that just stopped working in a young couple’s flat. Every call could be a routine bleed-and-fill or a full-scale hands-on puzzle in a heritage building with ancient pipes of unknown origin.
Most techs will see four or five jobs on a busy day, sometimes up to twelve during extreme cold snaps when boilers fail under pressure. Each visit starts with a rapid-fire assessment: is this safe, urgent, fixable, or a replacement nightmare? Systematic checks come next—visual inspection, pressure readings, firing cycles, leak checks with sensing sprays, gas sniffer passes for CO, and internal circuit diagnoses using multimeters. They’re always looking for patterns: odd knocking noises, pressure drops, or circuit board lights that don’t add up. Years in the trade mean knowing when something’s 'off' even when every gauge looks good.
Lunch? If there’s time. More often it’s a sandwich wolfed down between calls, hands still greasy. Emergency repairs aren’t just about skill—they’re a logistical blitz. Waiting on parts, phoning distributors, ducking back to the van for a specialty tool, and sometimes sharing notes with colleagues on Team chats, hunting for a fix to a system none of them have seen in years. Don’t forget the paperwork: after every job, detailed notes and customer reports are logged, both for regulations and for warranty claims that might roll in down the line.
Techs also spend time mentoring newcomers—apprentices shadowing them, watching for subtleties. It’s a profession of never-ending learning. New models, government regulations, greener technologies—there’s always a training session lurking on the calendar. Some evenings are spent reading service bulletins or upskilling on heat pump hybrids or hydrogen-ready systems, because you can’t stand still in this trade. Customers expect old boilers to last forever, and the law insists that every fix keeps up with the latest safety standards.
The unpredictability keeps the job sharp. Boiler techs can be knee-deep in an easy valve swap one moment and then get a call to a carbon monoxide alarm, where the stakes are suddenly life-or-death. Rapid thinking, solid nerves, and a knack for customer care keep them at the top of their game. It’s a job that attracts natural problem-solvers, the kind of people who’d rather be busy than bored—and who've never met a mechanical riddle they didn’t want to solve.
Tips for Finding the Right Person to Fix Your Boiler
The stakes can’t be overstated—a botched boiler repair is more than inconvenience; it’s real safety and lots of money on the line. So, how do you make sure you’re hiring a person who knows what they’re doing? Start with the non-negotiables: for gas boilers in the UK, demand proof of Gas Safe Registration; in the US, look for NATE certification or a state HVAC license. If a technician hems and haws or arrives 'just to have a look' with no ID, send them packing. Credentials matter for more than just paperwork—they keep you legal and safe.
Next, ask about real experience. Maintenance on modern condensing boilers is totally different from repairs on 30-year-old systems, so find out what models and brands the tech has worked with. Reliable companies publish reviews, show off before/after case studies, and make guarantees. Don’t get dazzled by the cheapest quote—a too-low price often means corners cut. You want transparency on pricing and clarity on what’s covered (labor, parts, warranties?). And check their response times: a good tech always has capacity for urgent calls, not just routine tune-ups three weeks out.
Ask smart questions when you call. Here’s a short list to get you started:
- Are you certified and insured for boiler repairs? Can I see your card?
- What brands do you specialize in?
- Can you explain the likely issue before you arrive, based on symptoms?
- How do you handle emergencies?
- Will you provide a full job sheet or invoice with details of work completed?
Practical tip: snap a photo of your boiler’s model and serial number before you call—that info gives techs a head start on diagnostics and part-hunting. Never ignore signs of trouble: banging sounds, pressure drops, water around the base, or repeated system resets all mean you need an expert, pronto. DIY repairs might be tempting but can void warranties, trigger safety failures, or even break the law.
Word of mouth still rules. Online reviews are handy, but neighbors who've had their systems fixed through the worst cold spell know the real stars. Check for trade association memberships or awards—yes, many of the best techs get recognized for their commitment. If you’re facing a complex system, ask for references or evidence of advanced manufacturer training. Honest techs are proud to show off their certifications and training history. And don’t be shy—ask to see the inside of their van. The tidier the tools, the sharper the tech.
Finally, get in the habit of annual servicing with a reputable engineer. Prevention is worth pounds, not just pennies, and having a pro spot problems early means you're far less likely to experience those cold, panicked mornings with a broken boiler. Experienced techs often offer service plans, spreading the cost and keeping your warranty intact. Smart homeowners know it’s better to build a relationship with a trusted technician than to gamble with urgent repairs in winter’s fiercest freeze.
Write a comment